Welding aluminum: challenges and solutions for perfect welding
Welding aluminum is a complex process that poses special challenges due to the unique properties of the material.
In TIG welding, two metal parts are melted together and thus joined inseparably. Welding is a technique that generally requires a certain amount of experience.
Welding light metals such as aluminum in particular requires extreme precision, the necessary caution and patience, experience and the right tools to guarantee a strong joint.
It is therefore always advisable to check at the planning stage whether another, easier to process material can be used for the construction, e.g. stainless steel/V2A, as this material:
- is better and easier to weld than aluminum alloys.
- has a higher stability with a thinner material thickness.
- withstands a higher thermal load.
- provides better traction due to more dead weight with thinner material, e.g. in model making.
The welding process for micropulse welding is started by lightly touching the workpiece with the electrode tip. The welding process itself takes place automatically and requires no further operator intervention.
Lampert’s precision welding technology delivers precise weld seams with maximum accuracy, minimal thermal stress on the workpiece and low deformation.
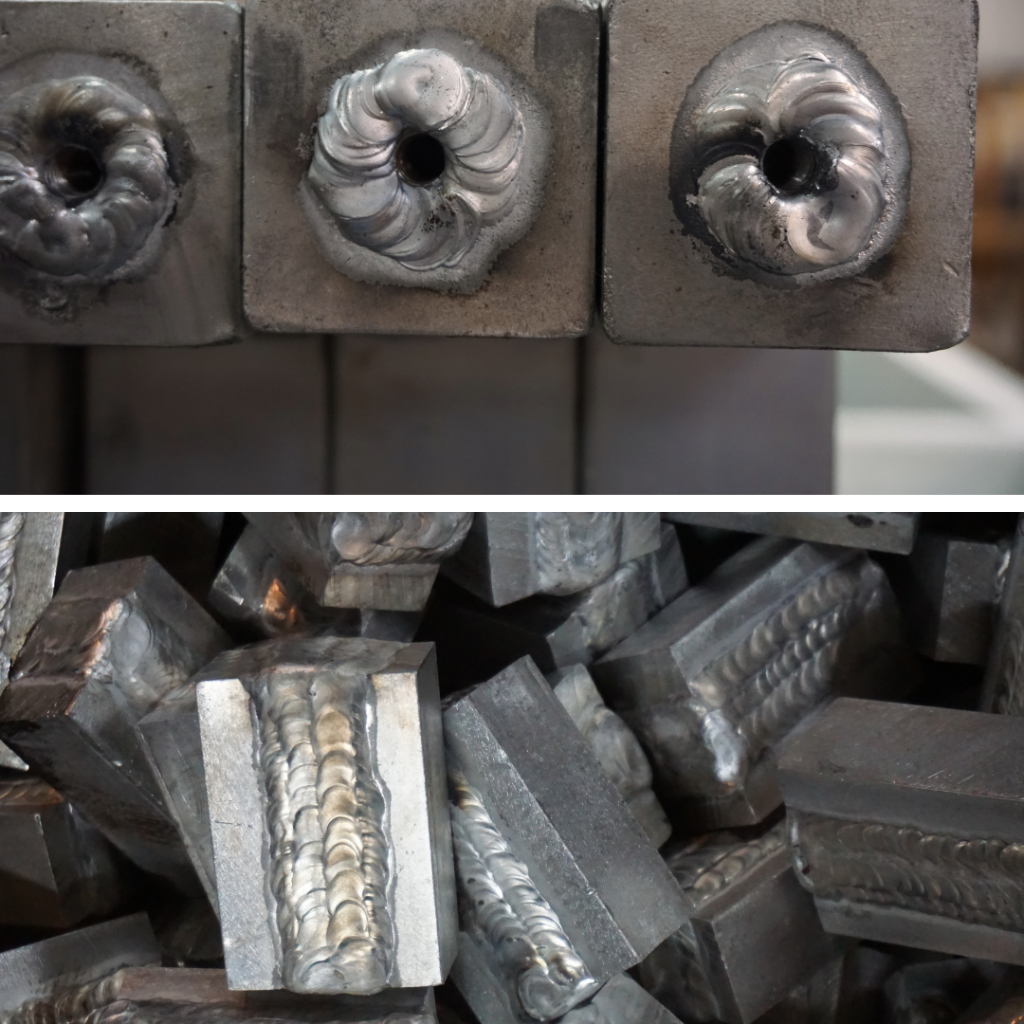
Can aluminum be welded?
Yes, you can weld aluminum. A special aluminum mode is stored in the current Micro Arc Welder model.
With this mode, aluminum alloys suitable for welding can be welded particularly well by feeding in welding wire. It is important to choose the right welding wire.
- The alloys AlMg3 and AlSi, for example, are suitable for aluminum welding with the Micro Arc Welder.
- If possible, the material designation should be known or obtained in order to be able to make an assessment of the weldability of the metal.
In general, there are a few basic things to consider in order to achieve good results for the workpiece when welding aluminum:
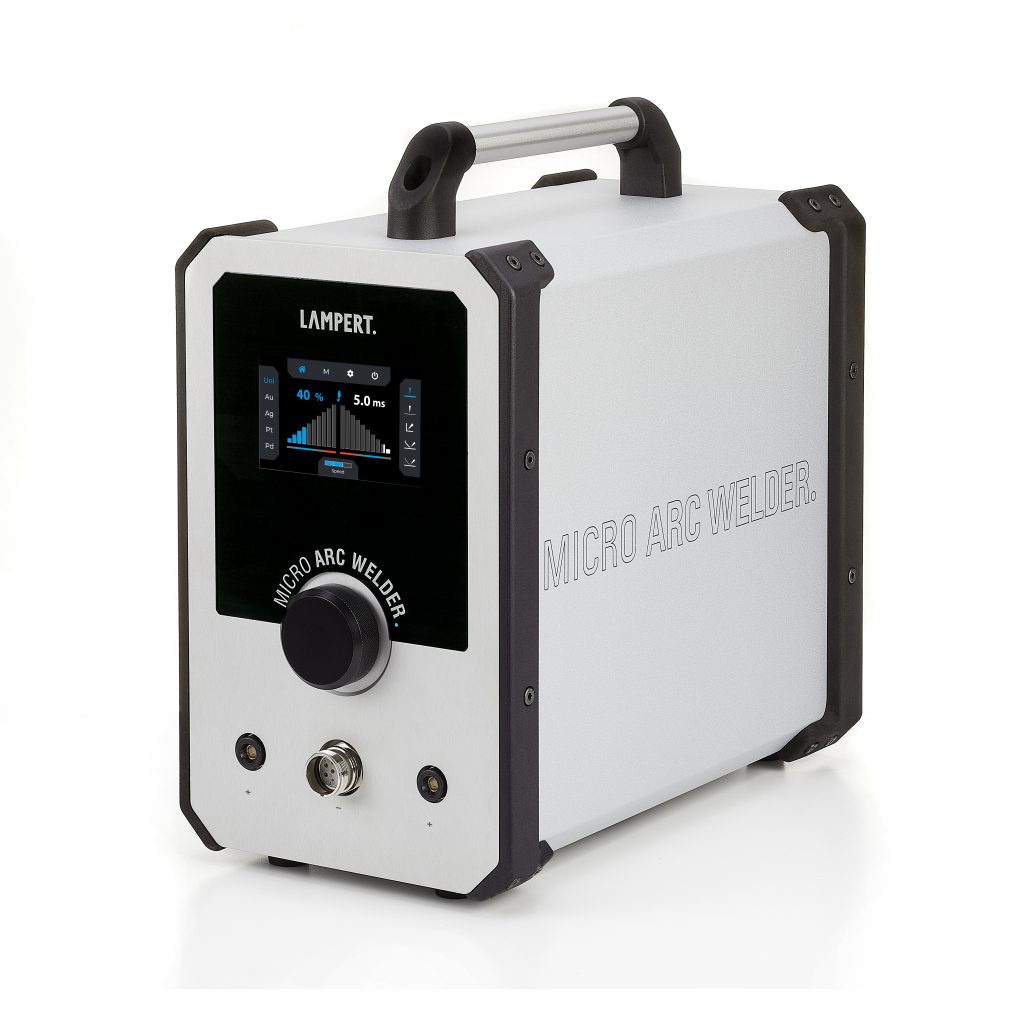
Preparing workpieces for aluminum welding
Aluminum base material forms an oxide layer as soon as it comes into contact with oxygen. The melting point of the oxide layer of aluminum is approx. 2050°C, while that of the base material is only 550 – 660 °C.
The oxide layer can form again within a very short time simply by touching the surfaces. It is therefore essential to always remove these before aluminum welding and after longer breaks.
This can be done mechanically, e.g. using a triangular scraper or an abrasive fleece. The workpieces should then be cleaned with a commercially available acetone-based brake cleaner to remove all possible contamination before welding.
The welding time and welding power settings
When TIG welding aluminum (alloys), it is generally advantageous to keep the welding time in ms lower and to slightly increase the welding line in %.
It is absolutely essential to keep the workpiece temperature as constant as possible when welding aluminum, but not too high and not too low. In practice, this means setting the spot welds continuously, as quickly as possible and at a constant speed.
Constantly interrupting the welding process can easily lead to stress cracks in the surface of the workpiece or the entire weld seam.
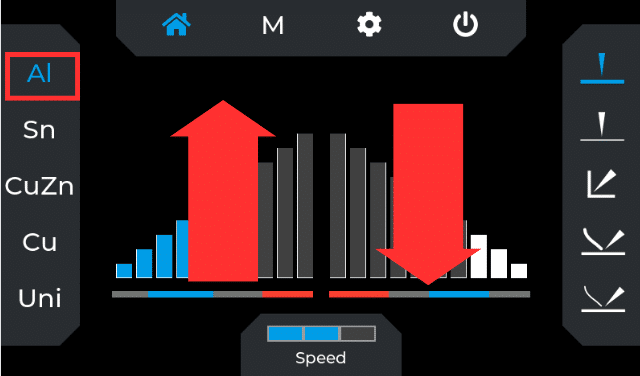
Possible inert gases for aluminum welding:
-
Argon, e.g. 4.6, i.e. with a purity of ≥ 99.996 %, is suitable for welding aluminum
-
Argon-helium mixed gases:
These mixed gases have the effect that a higher arc energy is transported during welding, i.e. this results in increased penetration into the material due to a higher arc voltage compared to argon.The most commonly used mixtures are 75 % Ar + 25 % He or 50 % each Ar + He.
Always remove sharp edges
When welding I-joints, sharp edges should be removed mechanically, e.g. by grinding. A flawless root can be achieved during welding by lightly chamfering the lower edges of the workpieces.
Increased stability through the use of welding wire
To ensure high stability when welding aluminum, it also makes sense to insert suitable welding wire into the weld seam, e.g. the following wires from our welding wire range:
- Welding wire AlSi (Art. No. 304 326)
for joining and surfacing aluminum-silicon alloys up to 12 % silicon and for different types of aluminum alloys with each other - Welding wire AlMg3 (art. no. 304 325)
for surfacing AlMg alloys with up to 3 % magnesium content
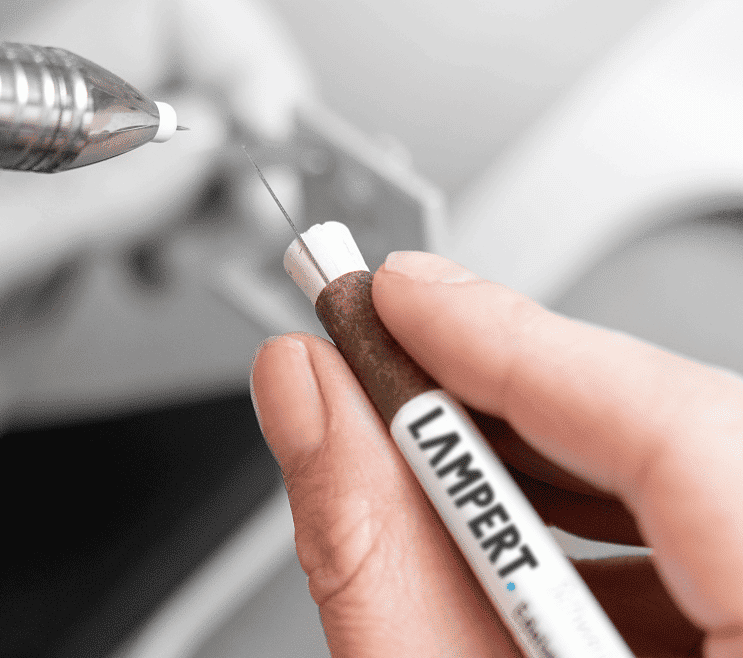